Bone china is rightfully considered "royal" - thin, snow-white, ringing, translucent … The only factory in Russia that produces such dishes is the Imperial Porcelain Factory. How and from what is such porcelain made, and why is it called bone porcelain?
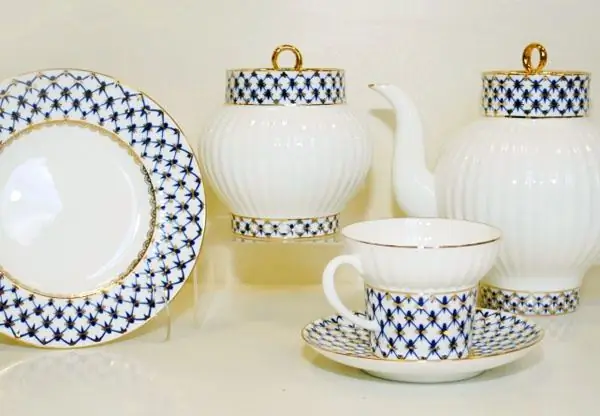
Porcelain "on the bones": a product of scarcity
The word "bone" in the name of the finest porcelain is not a metaphor, but a literal indication of the composition of the raw material. The usual porcelain mass consists of kaolin - white clay and other clay materials that give a white color when fired, as well as quartz and feldspar. In England, in the middle of the 18th century, they began to add bone ash to the composition - the calcium phosphate contained in it gave the dishes such incredible whiteness.
At the Imperial Porcelain Factory (in Soviet times, it was called Lomonosov), bone china began to be produced in the sixties of the XX century. It is paradoxical, but true: the reason the plant mastered this technology was not an ambitious desire to produce elite "royal" dishes, but … a shortage of raw materials.
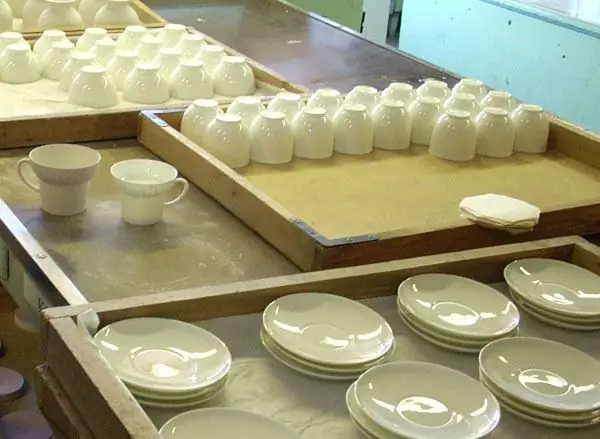
Since 1965, the plant experienced serious difficulties with the supply of kaolin - white clay was very widely used in the paper, perfumery and military industries. But there was a lot of bone waste in the country. Therefore, the director of the plant, Alexander Sergeevich Sokolov, set a task for the LFZ production laboratory: to develop the composition of the mass for bone china.
The composition of the raw materials was selected by trial and error (foreign colleagues were in no hurry to share commercial secrets). As a result, it turned out, for example, that bird bones gave the porcelain an unnecessary lilac shade.
As a result, we settled on the tibia of cattle. Moreover, there was no shortage of raw materials. The button production stamped from fat-free bones buttons for pillowcases and for military uniforms - and the waste went to a porcelain factory, where it was burned.
The mass for making bone china consisted of only 55% of traditional kaolin, clay, feldspar and quartz - the rest was bone ash.
In 1968, a bone china workshop was launched at the plant. Unlike English porcelain, which was quite thick, the LFZ decided to produce thin-walled porcelain. And at first they even "overdid it": the first cups turned out to be so thin and unrealistically light that customers began to complain about the feeling of "plasticity". Therefore, it was decided to increase the thickness of the shard by 0.3 mm.
The birth of "thin things"
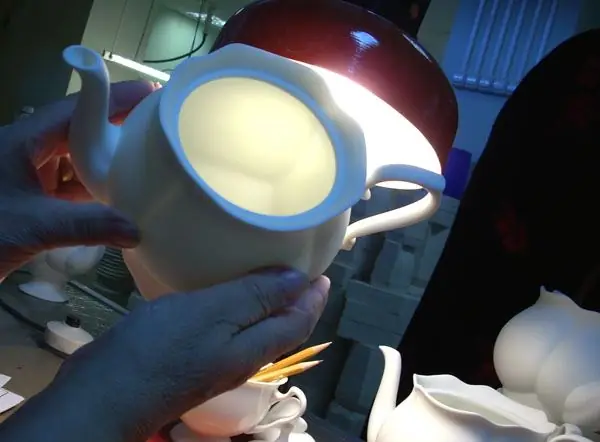
Bone china cups, like many other porcelain items, are made by casting. For this, the molds cast from plaster are filled to the brim with a liquid porcelain mixture resembling sour cream - a slip. Gypsum begins to "take away" moisture from the slip - and as a result, a porcelain "crust" gradually grows on the inner walls of the mold. When it gains the required thickness, the excess slip is removed from the mold. Then the dried "crock" (as unbaked porcelain is called) begins to lag behind the walls of the mold - and it is removed.
In the production of porcelain figurines, parts “gain thickness” for a rather long time - several hours. With thin-walled cups, everything happens much faster - at the Imperial Porcelain Factory, the bone china mixture is poured into molds for just two minutes.
Olive is automatic - the molds move in a circle, the required amount of slip is automatically poured out of the dispenser, and then the vacuum suction “takes” the excess.
Handles for cups, teapots, sugar bowls are cast separately and then "glued" by hand. The same porcelain mixture acts as an adhesive, only thicker.
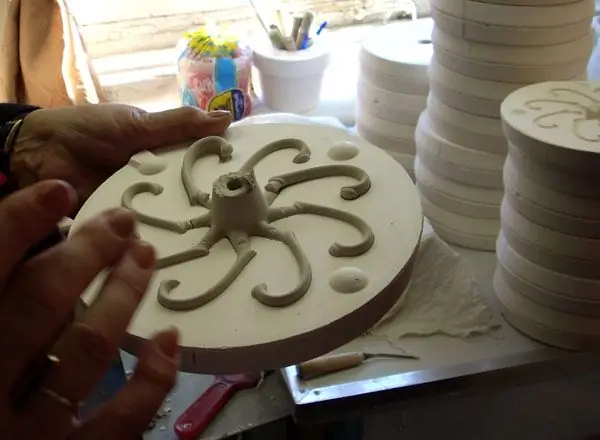
Flat products (saucers, plates) are made by stamping. A semi-finished porcelain product for such products is made very dense, it resembles a plastic dough rolled into "sausages". The cut piece of "sausage" is placed on a plaster mold, and a rotating forming roller is lowered onto it from above (each model has its own roller). The surplus is cut off automatically, but to grind the edges and make the surface absolutely flat is the task of the so-called "frames", who work only by hand.
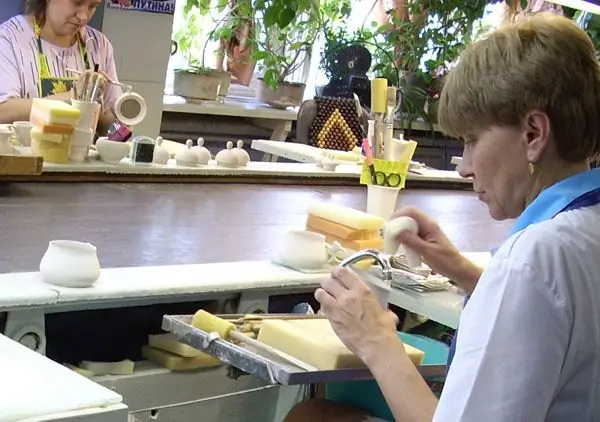
Sponge, brush, frosted glass, abrasive paper - the tools used by the frames are simple, but effective and time-tested. The porcelain headers get to them after drying.
How the shard is tempered
Bone china is fired twice. Moreover, the temperature for the first firing is very high - 1250 - 1280 degrees, which is much higher than that of ordinary porcelain. At this temperature, the porcelain mixture is completely "baked" and acquires the necessary strength. The dishes spend 12 hours in the oven. And, by the way, it decreases in size by about 13%.
But not yet shine. The shine will appear after the porcelain is covered with glaze. It consists of the same materials as porcelain, only in a different percentage, in addition, marble and dolomite are added to it. During firing, the glaze melts to form a shiny glossy surface.
The glaze is applied to the bone china using a spray gun - first on one side and then on the other side. And so that you can control the density and thickness of the layer, the glaze is tinted with magenta. Therefore, when going to the kiln for the final firing, the cups and saucers have a bright lilac color. At high temperatures, the pigment burns out and the porcelain turns white.
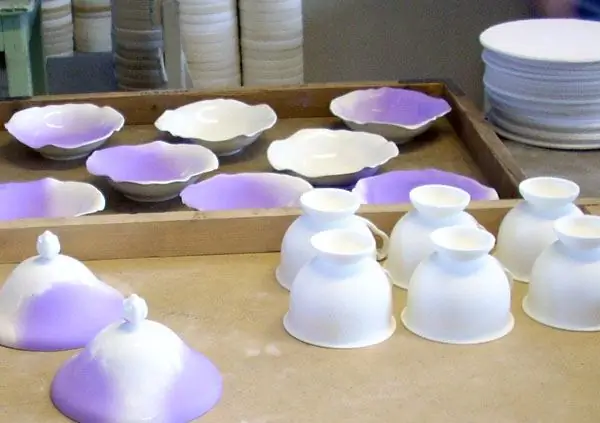
The second firing also lasts 12 hours, only the temperature this time is slightly lower - 1050-1150 ° C.
By the way, it was the firing temperature of bone china that became the reason that the Lomonosov Porcelain Factory managed to maintain a monopoly on the production of Russian bone china.
It was not customary among Soviet factories to keep the technology secret, therefore, in the early 70s, the technology and equipment designs were "presented" to the Bulgarian Republic, where a new porcelain production was launched at that time. And in 1982 the technology was transferred to a ceramic factory in Kaunas, Lithuania. But Russian factories did not dare to take up the production of bone china. The catch turned out to be that such porcelain is very sensitive to the firing temperature - and a deviation from the set temperature parameters by literally 10 degrees turns the dishes into scrap. At the same time, when it comes to temperatures over a thousand degrees, even the error of measuring instruments can exceed these same 10 degrees. So LFZ remained the only manufacturer of "royal porcelain" throughout the country.
How does the pattern appear
Pure white, unpainted porcelain, which was not touched by the artist's hand, experts call "linen". But before getting to the counters of brand stores, the dishes must be decorated with a pattern.
Painting on porcelain can be underglaze, overglaze and combined, combining both of these techniques. In such cases, the drawing is applied in two stages. An example of a combined painting is the famous "Cobalt Net" pattern, which has become a kind of "visiting card" of the plant.
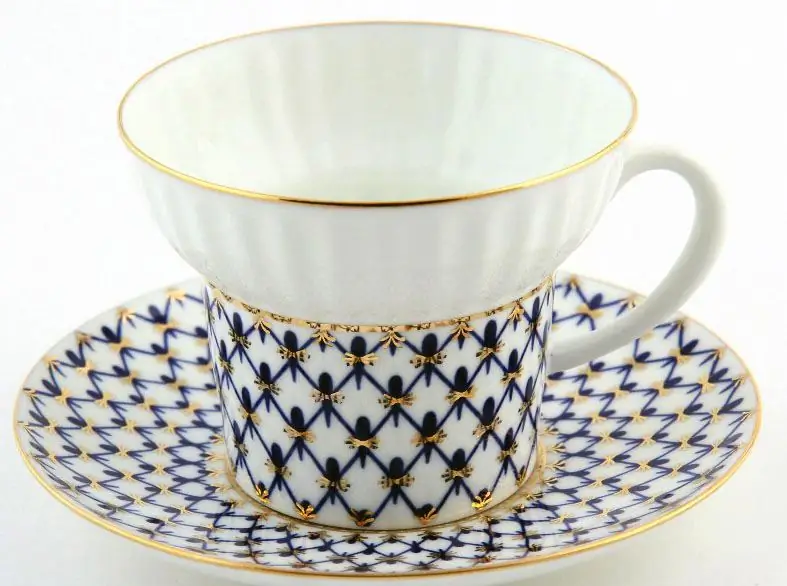
The cobalt pattern - blue lines - is applied to the porcelain even before the glaze is coated - during high-temperature firing, the decor is "fused" into the transparent glaze tightly. Cobalt, which before firing has a dull, dull black color, magically changes when heated, and depending on the concentration, the pattern becomes pale blue or deep blue. By the way, all paints used in underglaze painting behave in the same way - their color "appears" during temperature exposure, and when drawing a picture, they look faded - shades of black, gray, brown. And artists who work with several colors at once have a hard time: they constantly have to “keep in mind” the future picture.
The drawing is often applied by hand, but this work can sometimes be made easier. At the Imperial Porcelain Factory, for example, they developed special forms for dishes that will be decorated with a "cobalt mesh": thin, barely noticeable grooves are "drawn" on the sides of the shard - a kind of contour that must be manually "outlined" with cobalt lines.
The cobalt pattern can also be applied to the product using a decal - a thin film resembling a decal, on which a cobalt pattern is printed.
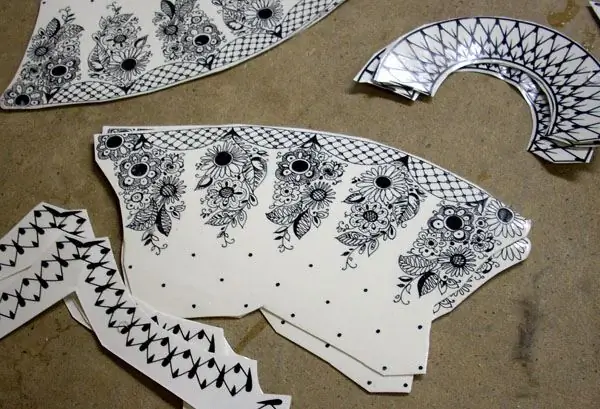
The shape of the decal exactly matches the shape of the dishes - it is different for each model. When heated, the film burns out, and the pattern is imprinted on the surface of the product.
The underglaze pattern is applied after the products have passed the first firing - and before glazing. After the second firing, such dishes sometimes look very strange - the first part of the painting has already been applied to it, and the second is still waiting in the wings. But you can already imagine what it will look like.
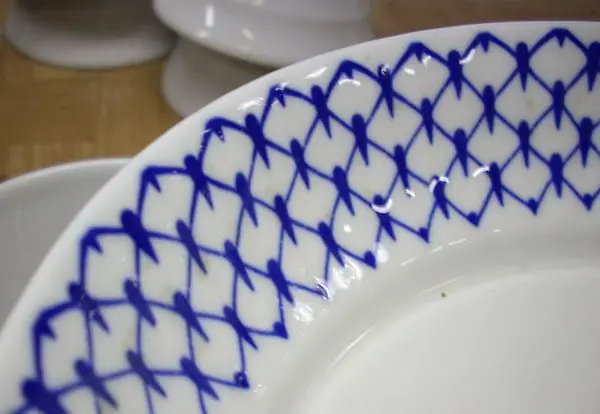
Painting with gold is already overglaze painting. Then the dishes will go through another firing, but at lower temperatures - only in order to fix the pattern. This is what makes it possible to use precious metals in painting, as well as many paints that cannot stand "four-digit" temperatures. Gold stars can be applied to the corporate design by hand, with a brush, or using a miniature stamp.