The first step in the functional tuning of domestic cars is to increase the power of the power unit. There are several ways to increase the engine size, although in most cases they are combined.
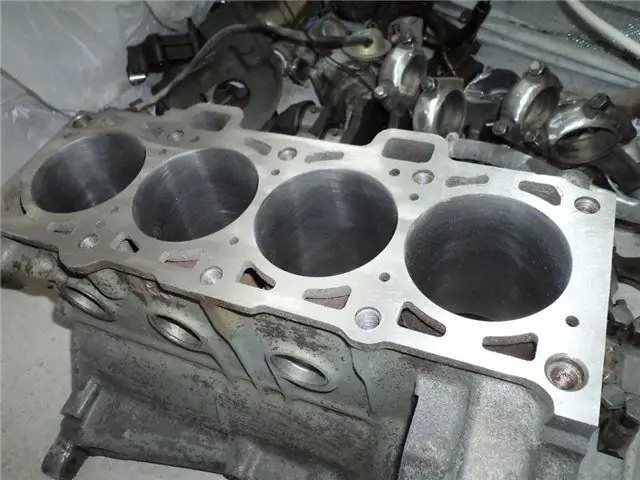
Forcing the engine is not as painless as it might seem at first glance. First of all, you need to take into account the economic feasibility of this operation. Experts, based on practical experience, consider it reasonable to increase the engine volume by no more than 25% of the original. If a more tangible increase in power is required, you should think about installing a new power unit. The main factors hindering unlimited expansion of the working area are:
- the requirement for a sufficient thickness of the cylinder block walls to prevent metal destruction during detonation;
- the mass of the cylinder block is sufficient for efficient heat removal from the working area;
- close location to the working area of the cooling system channels;
- inability of the engine lubrication system to increased loads.
These nuances should be taken into account when increasing the engine volume at the VAZ. In this regard, there are several ways to achieve this goal.
Boring cylinders to the required diameter
Engine cylinder boring is a completely standard procedure that is used during overhaul of the power unit, carried out in order to eliminate the gap between the elements of the piston system, which has increased due to wear during prolonged operation. Naturally, the degree of boring is severely limited by some conditions that cannot be neglected. To increase the resistance of metal walls to deformation, a special treatment of the inner surface is used or liners made of durable and refractory materials with high thermal conductivity are pressed into the cylinders. It is important to note that such operations are very expensive. In any case, cylinder boring is always associated with the completion of the engine cooling system.
Shortening the connecting rods
By shortening the connecting rod strut, an increase in the height of the working area can be achieved when the piston is at bottom dead center. Naturally, this leads to insufficiently high pressure of the air-fuel mixture during the compression stroke, which can be compensated for by installing turbo-compression fuel injection systems. It is quite possible to combine a slight reduction in the length of the connecting rod with the flashing of the electronics of the control unit for the fuel supply system on engines with injection injection.
The use of pistons with reduced thickness
Just one mistake when replacing engine pistons with thinner ones can lead to ultra-rapid wear or complete destruction of the power unit. There are two resulting disadvantages: a reduction in the distance between the oil scraper and compression rings, as well as a decrease in the strength of the piston itself. The first problem can be eliminated by reworking the engine lubrication system and using custom-made high-strength rings. To increase the strength characteristics of the piston, you need to think about special chemical and temperature treatment of metal, or about modernizing the design of the inner cavity of the working body. In the latter case, additional ribs are soldered to the inner walls of the piston, increasing the deformation resistance and improving heat dissipation.