Open-hearth furnace - equipment for smelting steel of a given composition and quality from scrap iron and pig iron. The open-hearth furnace got its name from the name of the inventor - the French engineer Pierre Martin, who developed it in 1864.
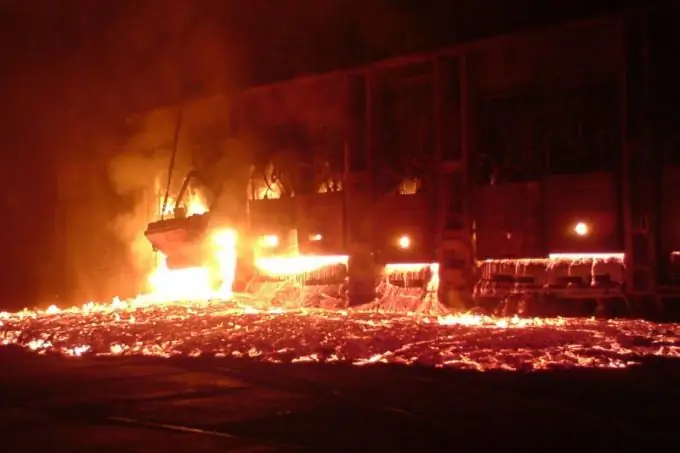
Technology
The key to the technology of converting cast iron into steel is to reduce the concentration of carbon and impurities. To achieve this goal, a method is used for their selective oxidation and removal into slags and gases during smelting. Steel smelting takes place in the following stages: melting of a mixture for smelting, consisting of scrap, coal, fluxes (charge), and heating a bath of liquid metal. The main goal is phosphorus removal. The stage takes place at a relatively low temperature. The next stage is the boiling of the metal bath. It takes place at higher temperatures of about 2000 degrees. The goal is to remove excess carbon. And, finally, steel deoxidation, iron oxide reduction.
The duration of the entire smelting process is 3 - 6 hours, natural gas or fuel oil is used for fuel.
A few facts from history
The converter processes for the production of cast steel that existed at the end of the 19th century did not allow the production of steel in large volumes and provide the specified characteristics. The huge stocks of cheap iron scrap accumulated by that time in the industry pushed metallurgists to search for a more productive and cheaper technology for processing scrap iron, as well as pig iron into steel.
This problem was successfully solved by the hereditary metallurgical engineer Pierre Martin, who received cast steel in a fired furnace at a factory in the French Sireil in 1864. The idea was to obtain liquid steel by melting scrap and cast iron on the hearth of a reverberatory furnace. The success was facilitated by the application of the invention of the brothers Williams and Friedrich Siemens on the recovery of heat from exhaust gases. The method of heat recovery consisted in the fact that the heat of the combustion products passing through the regenerators was accumulated in the nozzles and, together with the fan air, returned to the working zone of the furnace. Recovering the heat of combustion products made it possible to increase the temperature in the furnace to the values required for smelting liquid steel.
Worldwide success
The open-hearth process was quickly introduced into industry by all industrially developed countries of that time. The open-hearth method took a leading position due to its technological flexibility, scalability, controllability and the ability to obtain all the then known steel grades. With the development of technology for processing high-phosphorous cast irons, its importance has increased even more.
Of course, the first open-hearth furnaces had an imperfect design. The vaults were fragile. The hearths of the furnaces had a very short service life. The working space was not long enough, the bathrooms were too deep. Over time, the vaults began to be made more straight, which increased the durability of the furnaces.