Porcelain began to be transported to Europe from China in the XIV century, and it was valued at its weight in gold, and sometimes much higher. Even the shards of cups were worn as expensive jewelry at that time. European alchemists have been looking for the secret of making "white gold" for a long time, but the first European porcelain manufactory appeared only in 1708 in Saxony, in the city of Meissen.
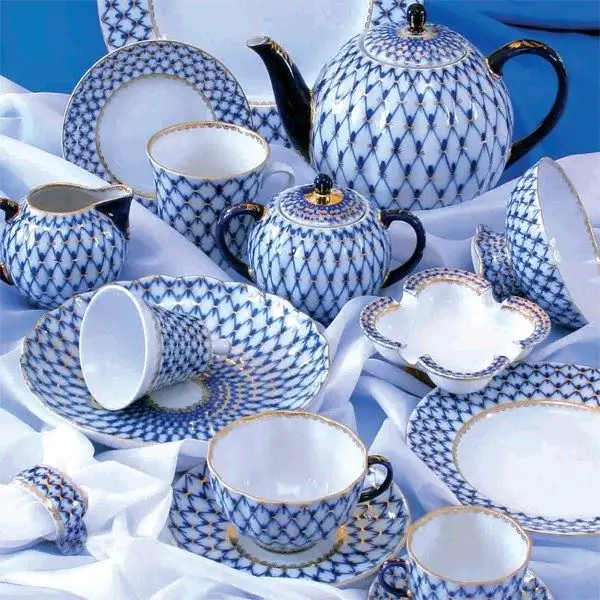
How the Imperial Porcelain Factory was founded
Porcelain production could not fail to interest Peter I, who strove to keep up with the West and dreamed of organizing a porcelain manufactory in Russia. He even sent people to Saxony on "espionage assignments." But the Meissen craftsmen did not succeed in "taking on the swoop" of the production secrets - they were tightly guarded. And Russian porcelain began to be produced only under Elizabeth.
On February 1, 1744, the chamberlain of Empress Elizabeth Petrovna, Baron Nikolai Korf, entered into an agreement with a certain Christopher Gunger, who undertook to "establish a factory in St. Petersburg for making Dutch dishes." And six months later, a factory for the production of porcelain was founded near St. Petersburg (this is what porcelain was called in Europe at that time). But at the same time, Gunger could not establish production: he actually did not have either knowledge or skills.
The case was saved by the so-called "student" of Gunther - Dmitry Vinogradov. Before entering the manufactory, Vinogradov studied chemistry, metallurgy and mining for eight years in Europe - and it was he who, in 1746, managed to obtain the first successful samples of Russian porcelain, and then to perfect the production technology and put it on stream. In 1765 the manufactory was named the Imperial Porcelain Factory. After that, for a century and a half, the factory, which from the first day specialized in the production of artistic porcelain of the highest quality, worked mainly on a "government order". The sets, vases, painted dishes produced here could not be bought - only received as a gift from the emperor.
Pages of history: propaganda porcelain and teeth for the Soviet regime
In the post-revolutionary year 1918, nationalized and renamed the "State Porcelain Factory", the enterprise came under the jurisdiction of the People's Commissariat for Education, and the ideological task was set before it: the development of products "revolutionary in content, perfect in form, impeccable in technical performance." The result was the famous propaganda porcelain, which became “concurrently” also a new stage in the development of the Russian avant-garde.
Under the leadership of the artist Sergei Chekhonin, a whole galaxy of artists took part in the creation of propaganda porcelain, including Petrov-Vodkin, and Kustodiev, and Malevich, and Kandinsky.
In 1924, when the country was thinking about restoring the national economy, the enterprise was transferred under the management of "Farfortrest" - and the main forces were thrown into the production of technical porcelain. The plant, which was named after Lomonosov in 1925, produced more than 300 types of products: dentures, artificial eyes, insulators, boilers, laboratory glassware, and so on.
Despite this, the enterprise remained a "supplier of the yard": at the ceremonial receptions, the Kremlin tables were served with dishes made by special order by the masters of the LFZ. And in the 1930s, the first art laboratory in the country was opened at the plant (it was directed by Malevich's student, Suprematist artist Nikolai Suetin), which created the style of “Soviet porcelain”. And in the "thaw" of 1953, dentures were forgotten: the plant began to satisfy the "needs of the Soviet people" to bring culture into everyday life, specializing in the development of new technologies and the production of products of increased complexity. And in 1965, the famous bone china began to be produced here.
After the collapse of the USSR, the Lomonosov Porcelain Factory was privatized and for some time teetered on the brink of closure, but then gradually "came to its senses." In 2005, the enterprise regained its historical name and again became "Imperial", took a clear benchmark for the production of "luxury" products, products for individual orders and artistic porcelain.
"Trademarks" of the Imperial Porcelain Factory
Bone china is rightfully considered "royal" - incredibly thin-walled, ringing, translucent. It began to be produced in England in the middle of the 18th century, adding bone ash to the porcelain mass - the calcium phosphate contained in it and giving the dishes such an unprecedented whiteness. The St. Petersburg Imperial Porcelain Factory is the only enterprise in Russia that produces such porcelain. At first it was only tea and coffee cups and saucers, since 2002 sets have been produced.
The plant's technologists selected the composition of raw materials for bone china by trial and error. As a result, we settled on the tibia of cattle. At first, bone china was made from button production waste.
Another "distinction" of the IPZ is an artistic sculpture made of porcelain, which is produced by hand. On average, it takes a craftswoman 2-3 days to cast one figurine. Porcelain "dolls" - figurines of people and animals - have been produced here since the middle of the 18th century. One of the most famous pre-revolutionary series of sculptures is "The Peoples of Russia" (about a hundred figures depicting men and women in national costumes), of the Soviet sculpture, the most famous is the "ballet" series. Now in the art sculpture workshop of the LFZ, both "replicas" (repetitions) of historical figurines and new models are produced. Among the latest works, a series of sculptures by Mikhail Shemyakin, depicting the characters of The Nutcracker, has become especially notable.
Porcelain painting is what allows you to turn “just a good thing” into a unique thing. The Imperial Porcelain Factory has two painting workshops: manual and mechanized. The hand-painted workshop employs about 20 artists who create unique exhibition porcelain and custom-made products. It can take about a month to decorate one vase or dish, and the cost of such items is extremely high.
The work in the workshop of mechanized painting is more monotonous, but it is here that patterns that are recognized all over the world are created. Among them is the "visiting card" of the IPE - the famous "Cobalt Net" - a pattern for the creation of which the factory artist Anna Yatskevich was awarded the gold medal of the World Exhibition in Brussels in 1958. Since then, crockery decorated with this pattern has been produced in the factory on an industrial scale. They even developed special forms for such dishes: on the sides of it, even during casting, thin grooves are "drawn" - a contour that must be manually "circled" with cobalt lines. Cobalt netting can also be applied to the product using a decal - a thin film resembling a decal, on which a cobalt pattern is printed. When firing porcelain, the film burns out, and the pattern is imprinted on the surface of the product. Gold stars at the intersection of the blue lines are applied to the pattern either by hand or using a miniature stamp.